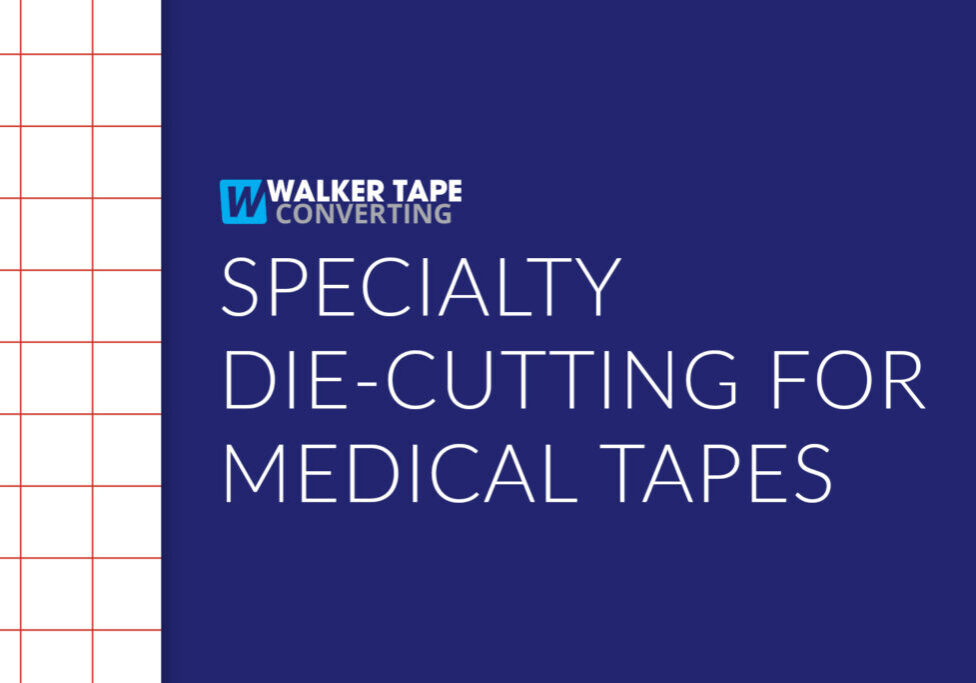
The medical industry is always changing and adapting. One thing that has stuck around for a little while in it is tape. Tape is used in so many different ways in the medical industry (which we’ll go over a bit later).
When picking the right tape for your medical uses, there are a lot of things that need to be considered. Things like the shape, size, and number of cuts can change how effective a tape can be. The wrong shape or cut could change how the tape works entirely.
This is why converting processes like die-cutting are so important for medical tapes. So, let’s go over what die-cutting can do for medical tapes together.
How Die-Cutting Could Make Medical Tapes More Efficient
First, let’s give a quick definition of what die-cutting is. It is a process that involves using a pre-shaped die to cut out shapes of tape. These cuts can go through specific layers of the tape, so that you can have different parts of it peel off rather than others.
You can read a bit more about the specifics of how die-cutting works and the different kinds of cuts in our blog. For now, let’s just focus on the ways that die-cutting can help medical tapes.
Specifically, die-cutting can make tapes better suited for devices and applications like:
- Electrodes
- Heart rate monitors
- Bandages and dressings
- Ostomy
- Medical drapes
- Hearing devices
- Any other devices or applications requiring specific adhesive shapes.
Die-cut tapes could help make each of these devices and processes more secure and effective.
As mentioned, die-cutting can do more than just cut out particular shapes in the tape. There are a few different levels of cut that can change how the tape is used. For example:
- Level 1 Cut: Cut all the way through the sheets, leaving individual pieces of tape.
- Level 2 Cut: Cut through the top liner and adhesive, but not the bottom liner. This leaves the shapes of tape all together on the liner.
- Level 3 Cut: Cut through only the top liner, making the top liner easy to remove.
- Level 4 Cut: Perforating through the tape.
We can do each of these on pretty much any tape. It’s also possible to do certain combinations of the different cuts to make the tape exactly how you want it.
Case Study
To show you how exactly we can use die-cutting to help out with medical tape, here is one of our case studies.
A company came to us with an existing medical device that had some limitations. While we were initially unfamiliar with the device, we were able to give them a custom solution for these limitations.
The company’s device was being used to conduct a 30-day study. This study required the device to stay on the subjects’ skin for the entirety of the study. But they found, as they tried to conduct the study that they were running into all kinds of problems like:
- The adhesive on their current tape was not strong enough to stay on for the full 30 days.
- The adhesive used to keep the device on the tape wasn’t strong enough to stay on during the study.
- The device-facing adhesive was also difficult to work with during production.
To help them out we decided to focus on one issue at a time. We started by adding several layers of material to the tape to add weight to it. This helped make it more usable for the staff during production and placing the device.
Then we made a custom adhesive that would hold the device to the skin for the full duration of the study. We made sure that the adhesive was kind on the subjects’ since it would have to stay on for about a month.
While looking more closely at the device, we determined that the adhesive being used to hold it to the tape was wrong. The surface of the device was a different kind of surface energy than what the adhesive was made to hold. This is why it wouldn’t hang on to the device for as long as needed. We worked with the company to find a good adhesive that would be able to hold the device for a long time without damaging it.
Finally, we used a custom die to cut the tape into the exact shapes that the company needed for their devices.
This all resulted into a thicker, sturdier, custom-shaped tape that stays on as long as needed and is easy to work with. Not only were we able to customize the make-up of the tape, we were also able to die-cut it to fit their specifications. This solved the company’s issues and limitations with the device.
This case is just one of many that show how we can help out with medical tape. However, there is one thing that is important to understand here.
At Walker Tape, we have the capabilities to help with several different problems. The one capability we don’t currently have is creating sterile tape. As you are likely aware, sterility is important for tapes that are used in certain applications. So, if you are looking for sterile tape, we may not be able to do that type of converting for you.
However, that doesn’t mean that we can’t help you at all. In the above example, we were able to help the company solve several of their problems by looking at the tape they were using. We were able to help identify where and how the tape could be improved.
So, while we may not be able to convert the tape for you, we can help you design your perfect tape. Plus, if you need medical tape, but you don’t need it to be sterile, we can help you with the whole process.
We’re here to help you make your product or project everything that it can be. So, reach out to one of our experts today. Let’s get started on making your perfect tape.