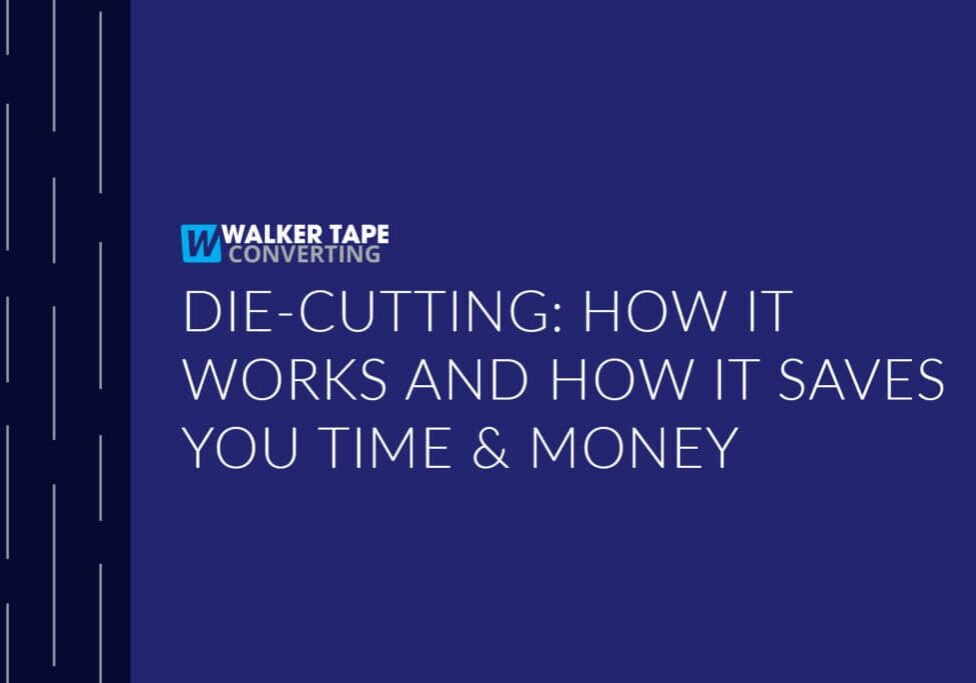
There’s a pretty good chance that you’ve heard of die-cutting before. It’s used in several different industries.
But just in case you aren’t familiar with it, die-cutting is using a premade piece to cut customized shapes out of a material. When it comes to tape, die-cutting is the best way to get the shape of tape you want. It is one of the most common processes in converting.
Here at Walker Tape Converting, die-cutting is one of the things that we do best. It’s one of the areas that we’ve focused on because it can help you save time and money.
Let’s talk about how it works.
How Die-Cutting works
The best way to think about die-cutting is to think of the dies as cookie-cutters. The blades can be made into whatever shape, like a semi-circle, and will press through layers of tape to cut out those semi-circles.
There are a couple of different kinds of die-cutting that you can choose from for your tape. Each different form of die-cutting has to do with how many layers the dies cut through. Which cut you want can depend entirely on what you are looking for in your tape.
Here are the main kinds of die-cutting you can choose from and combine to fit your needs:
-
- Cut all the way through the tape. This creates fully individual pieces of tape in the desired shape.
- Cut through top liner and adhesive. This creates cut out shapes lined up on one sheet, like stickers. This can also make the back liner longer and easier to remove.
- Cut only through top liner. With bottom liner and the adhesive untouched, the top liner is much easier to separate from the other layers.
- Perforate the tape. Using dies, you can create small holes throughout the tape.
With a more basic idea of how we do die-cutting, let’s get into some examples to help make it all clearer.
Examples of Our Die-Cutting
Below are photos of some of the die-cuts that we’ve done in the past, just so you can better understand what each kind of die-cut can do.
This custom shape of tape was made using a one-level die. It cuts all the way through each of the layers. This way, there are individual pieces of tape, consistently the same size and shape, ready for you to use.
A sheet of tape, like this one, is made using a two-level die. One of the levels cut through all of the layers, while the other cut through the top liner and the adhesive. This creates a full sheet of tape cut into individual shapes, which can be all the same or varying shapes.
Two-level dies can also make tapes easier to peel apart. For example, this strip of tape was made using a two-level die. One level cut through only the top liner and made peeling simple. Another level cut the holes through the liners and the adhesive.
Three-level dies can create even more complex cuts. This sheet, for example, was made using a three-level die. One level cut the shape out of the adhesive, while another cut the circle shapes out of the top liner, leaving the back untouched. Finally, the third level cut the live through the top liner to make it simple to peel.
As you can see, there are a lot of different ways that die-cutting can be done. You can fully customize the shape of the tape and which layers can peel away.
All you need to do is work with us on how you want it and we can make it for you.
A Case Study in Die-Cutting
With the way that die-cutting is so customizable, it has an incredible ability to help your company save time and money. But you don’t have to take our word for it. Let’s go over a case study of how die-cutting helped one of our clients.
A little while back, we were approached by a company in the medical industry that wanted a better way to produce a custom product.
The product was made by laminating seven different materials together by hand. Then it would be die-cut by hand and finished into the final product.
As you can probably guess, this was very time consuming, with a lot of room for human error. So, they came to Walker Tape Converting looking for a way to streamline this process. We were able to show them the initial savings in raw material cost alone.
Through our large network, we were able to find that just two materials could be combined to get the same result as the seven they had been using. We were also able to get these materials for them at a significantly lower cost than what they had been paying before.
With the materials ready to go, we were able to completely automate the processes of laminating and die-cutting. This made the work faster and much cheaper, and also eliminated the chance of human error.
Before it took them five minutes to make one product. We helped them to produce 250 products in five minutes.
With our resources, we were able to save them over $200,000 dollars a year in labor, production, material, and waste costs.
That’s just one example of the many ways that we’ve been able to help our clients save time and money with converting and die-cutting. You can read more about how we may be able to help your company on our blog.
If you don’t need to hear any more and are ready to get started, head over to our contact page. There you can find the resources you need to get ahold of our team of experts. They can get you a quote and answer any questions you may have.
It’s time that you make working with your tapes that much easier by getting them die-cut. We at Walker Tape Converting will be happy to help you with it.