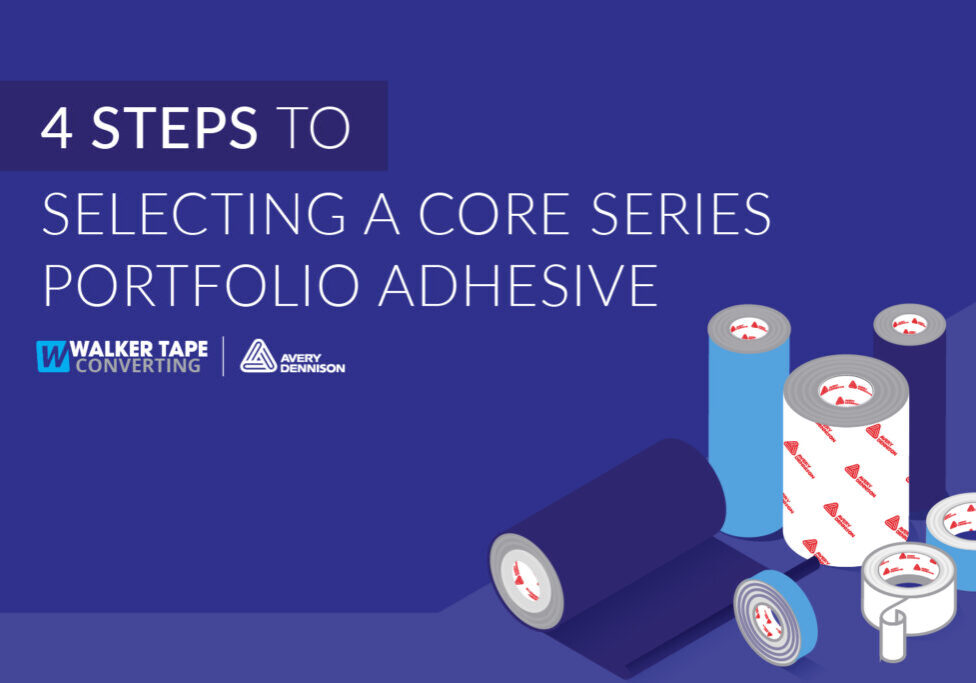
AVERY DENNISON’S CORE SERIES™: SIMPLIFYING ADHESIVE CONVERTING DOWN TO FOUR HELPFUL STEPS
Over the years, we’ve formed excellent relationships with Avery Dennison to make sure you always have access to the widest range of quality materials. Just as we begin thinking those bonds are as strong as they could possibly be, they release the Core Series™ Portfolio.
To put it subtly: we’re thrilled!
Over the years, we’ve formed excellent relationships with Avery Dennison to make sure you always have access to the widest range of quality materials. Just as we begin thinking those bonds are as strong as they could possibly be, they release the Core Series™ Portfolio.
To put it subtly: we’re thrilled!
One of the best perks of the Core Series™ includes a selection process for us to find precisely the tape solution you need in four brilliantly simple steps:
- Lamination
- Surface Energy
- End-Use Requirements
- Tape Construction
These steps make the research phase easier and the entire selection process better from the initial quote request to the finished product.
The Bottom Line: We find you the perfect solution faster than ever before.
Step 1: Lamination
- What are you laminating to?
Do you need to put adhesive on foam, fabric, film, or foil? Whichever material you need, the Core Series™ Portfolio charts out how well all nine adhesive families laminate to the following tape carriers:
- Foams: Polyether urethane, polyester urethane, dense urethane (Poron®, HyPUR-cel®, Norseal®), sponge rubber (EPDM, PVC, Nitrile vinyl, Neoprene)
- Fibrous materials: Nonwovens, felts, fabrics
- Films and foils: High surface energy (HSE), medium surface energy (MSE), low surface energy (LSE)
Knowing how well adhesives laminate to various materials helps us pinpoint the most successful combinations. So, for example, if your application uses sponge rubber, we can narrow down which adhesives hold the strongest.
The Bottom Line: We match the best adhesive for the tape solution you need.
Step 2: Surface Energy
- What surfaces are you sticking to?
Whatever surfaces you bond to have a surface energy. The higher the surface energy, the easier it is to bond to. So, it’s vital that your adhesive works with the surfaces you need it to. With this in mind, the Core Series™ selection guide shows us how well each adhesive bonds to various substrates across a wide spectrum of surface energies:
- High: Aluminum, stainless steel, copper, glass, polyimide (Kapton®), nylon, polyester (PET), polyurethane (PU) film
- Medium: ABS, polycarbonate (PC), vinyl (PVC), acrylic, polystyrene
- Low: EVA, powder-coated paints, polyethylene (PE, UHMW), polypropylene (PP), PVF (Tedlar), unknown substrates
- Extra low: PTFE (Teflon®), silicone
Bottom Line: We precisely match the adhesive to the surfaces you work with.
Step 3: End-Use Requirements
- What are your application requirements?
Each project faces unique challenges, whether they’re environmental conditions, performance constraints, regulatory certifications, and so on. You may need the long-term shear strength of an acrylic adhesive, yet you may also have to keep VOC levels low, for example.
As we work with you to learn what your project requires, we can then easily find a solution that checks off all the necessary boxes with Avery Dennison’s selection guide. It compares the performance of all the Core Series options when considering the following traits:
- Maximum Service Temperature
- Humidity Resistance
- Solvent/Chemical Resistance
- UV Resistance
- Shear Strength
- Initial Tack
- Price
Bottom Line: We determine the exact adhesive that meets each of your application’s criteria.
Step 4: Tape Construction
- What tape construction do you need?
Tapes are surprisingly customizable. You may need transfer tape placed directly on your application, single-sided tape custom die-cut for masking jobs, double-sided tape with different adhesive on both sides meant to bond to two completely different kinds of materials. This list goes on.
This final step allows us to tailor your tape all the way down to the most practical liner. In fact, it provides which constructions and liner types work best in the following categories considering production and application processes:
- Tensile strength
- Tear resistance
- Conformability
- Humidity resistance
- Rotary die-cutting
- Kiss-cutting
- Water jet
Bottom Line: With Avery Dennison’s Core Series™ Portfolio and our custom capabilities, we make sure you get the right tape solution down to the very last detail.
Check out our latest Youtube video about the Core Series Portfolio here.
Conveniently add any of the products from Avery Dennison’s impressive Core Series™ Portfolio to a free quote request today.